Should I get a ceramic coating without paint correction first?
February 13, 2024
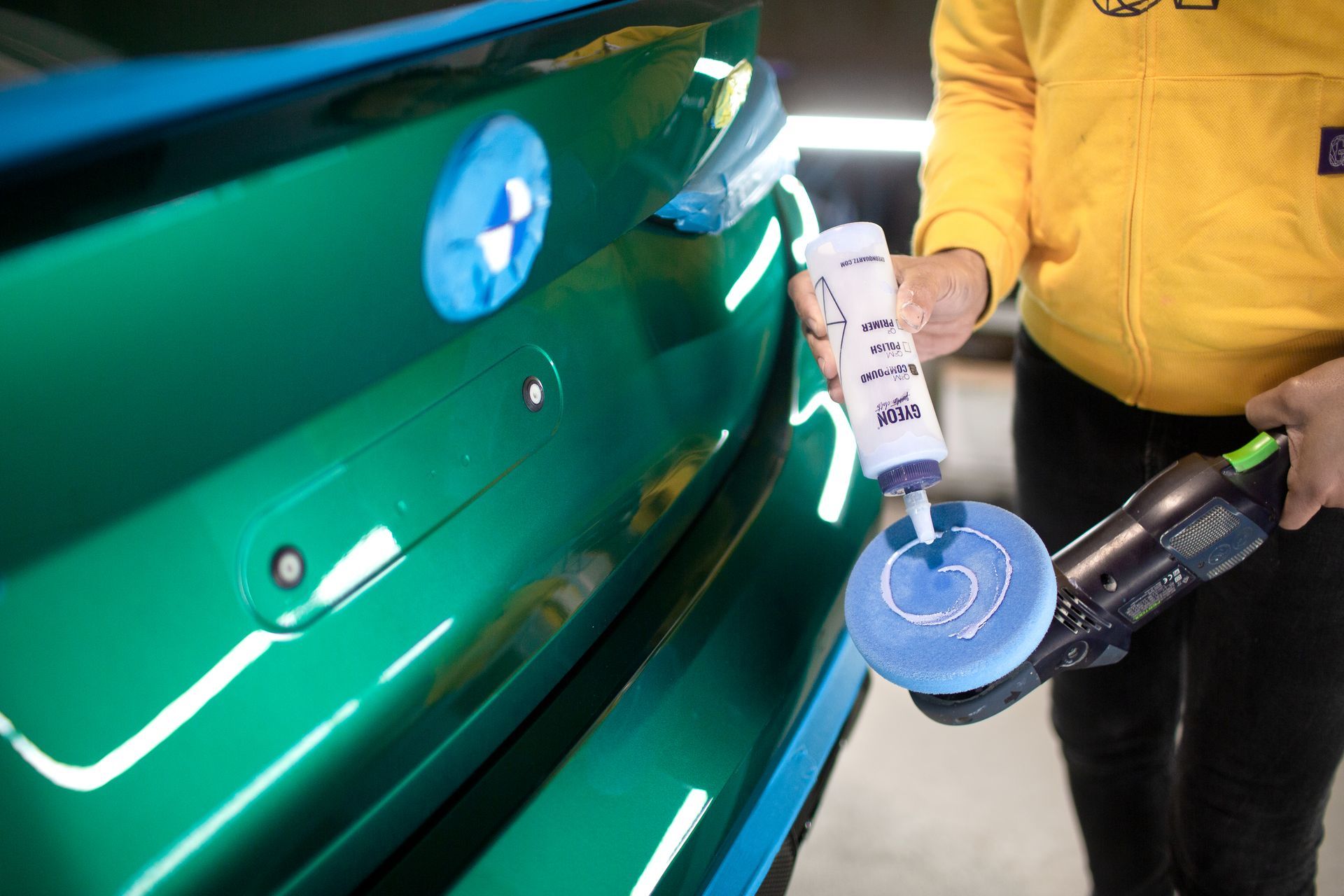
When considering a ceramic coating for your vehicle, one of the most common questions is whether paint correction is necessary first or if the coating can be applied directly. While manufacturers strongly recommend paint correction, some vehicle owners opt to skip it to save time and money. Let's dive deep into the implications of applying ceramic coating without paint correction.
Understanding Paint Correction
Paint correction is a meticulous process of machine polishing the clear coat using specialized compounds and polishes. The primary goals are:
- Removing swirls, scratches, and oxidation
- Eliminating water spots and etching
- Smoothing out orange peel texture
- Restoring depth and clarity to the paint
This process reveals a flawless, glass-like surface, preparing the paint for maximum bonding and durability from a ceramic coating.
Why Manufacturers Insist on Paint Correction
Most reputable ceramic coating brands specify paint correction as a required step before application. Here's why:
1. Ensures a Contaminant-Free Surface
- Compounds remove embedded contaminants that washing alone can't eliminate
- Prevents potential coating bonding issues
2. Eliminates Minor Imperfections
- Smooths away micro-scratches caused by improper washing or claying
- Prevents these flaws from being sealed under the coating
3. Enhances Coating Adherence
- The polished clear coat allows for better bonding and a more uniform coating layer
- Improves the overall effectiveness of the ceramic coating
4. Extends Coating Longevity
- Coatings typically last longer on properly corrected paint
- Reduces the risk of premature failure or uneven wear
5. Maximizes Gloss and Depth
- Corrected paint provides a better foundation for the coating to enhance
- Results in a more impressive final appearance
While high-quality coatings still offer protection without correction, following manufacturer instructions ensures optimal performance and longevity.
The Argument for Skipping Paint Correction
Some car owners choose to apply ceramic coatings directly, bypassing paint correction. Their reasons include:
- New Vehicle Assumption: Believing a new car's paint is flawless (often not the case)
- Budget Constraints: Avoiding the additional cost of paint correction
- Time Limitations: Unwilling to wait for the extra time required for correction
- Satisfaction with "Good Enough": Accepting less-than-perfect results for convenience
While these reasons may seem valid, it's crucial to understand the potential consequences.
Risks Associated with Skipping Paint Correction
Applying ceramic coatings without proper paint correction can lead to several issues:
- Reduced Durability: The coating may fail prematurely, often within 1-2 years instead of the expected 3-5 years or more.
- Adhesion Problems: Improper bonding can cause the coating to flake or peel unevenly.
- Hazy Appearance: Existing micro-marring in the clear coat gets sealed under the coating, resulting in a cloudy look.
- Enhanced Imperfections: The coating can actually highlight existing paint defects rather than hiding them.
- Staining and Discoloration: Surface contaminants locked under the coating can lead to visual distortions over time.
- Difficult Removal: Removing a coating applied to uncorrected paint is significantly harder and riskier, potentially damaging the paint.
- Uneven Protection: Areas with existing damage or contamination may receive less effective protection.
- Diminished Aesthetic Impact: The full visual enhancement potential of the coating isn't realized on uncorrected paint.
The Long-Term Perspective
While skipping paint correction might save money initially, it often leads to higher costs in the long run:
- More frequent reapplication of coatings
- Potential need for paint correction later, which may be more extensive
- Decreased resale value due to subpar paint condition
Professional Insights
Many professional detailers refuse to apply coatings without proper paint correction. They understand that their reputation is on the line, and they want to deliver the best possible results for their clients.
Conclusion: The Value of Proper Preparation
While it's technically possible to apply a ceramic coating without paint correction, both manufacturers and professional detailers strongly advise against it. Proper paint correction delivers:
- Superior protection
- Enhanced shine and depth
- Extended longevity
- Better overall value
The extra effort and cost upfront provide exponentially better and longer-lasting results. It's always advisable to discuss your options with a reputable detailing professional. They can assess your vehicle's specific needs and help you determine if paint correction fits your goals and budget.
Remember, when it comes to ceramic coatings, the quality of the foundation (your paint) directly impacts the quality of the final result. Investing in proper preparation pays dividends in the long run.
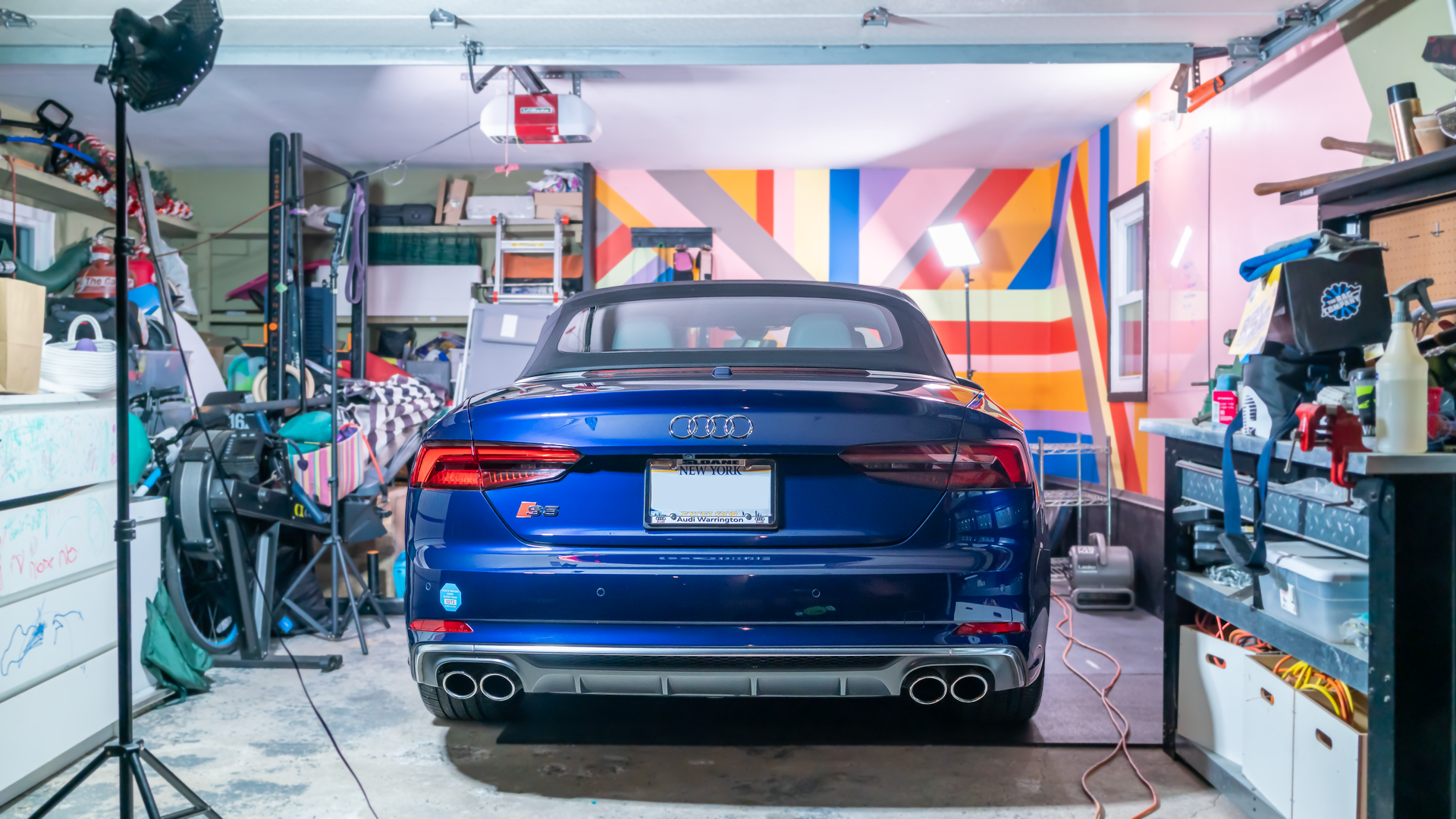
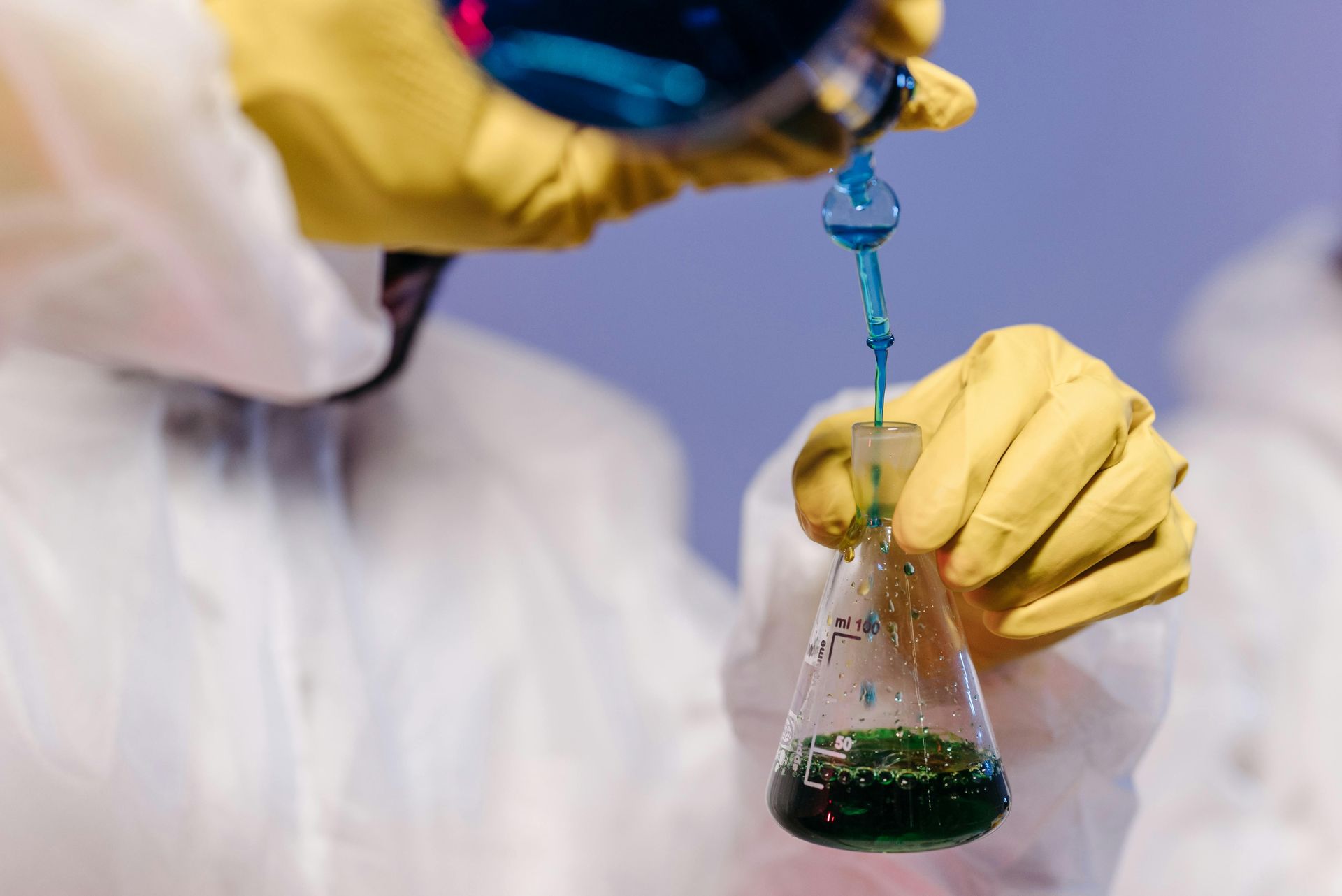
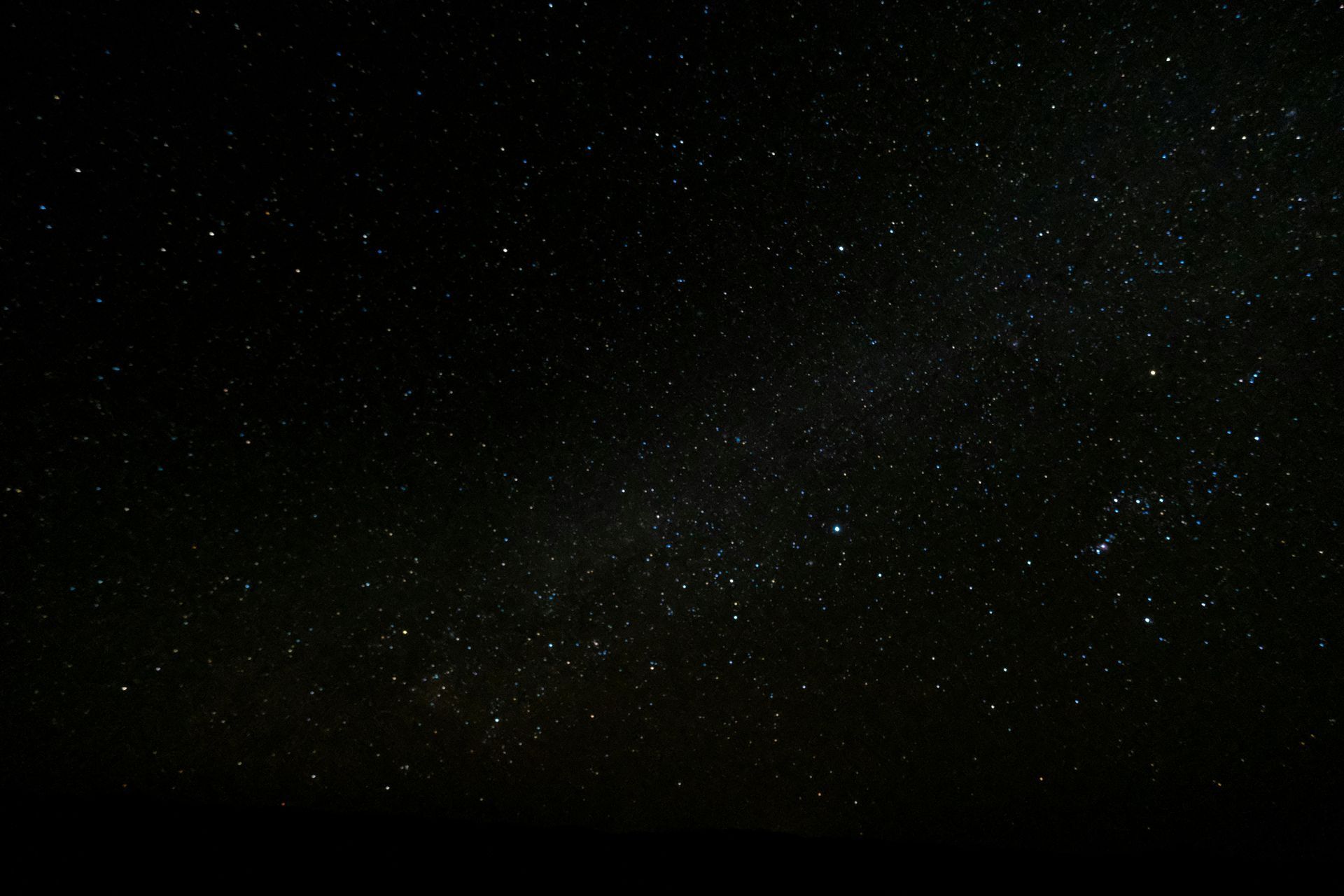