Understanding Ceramic Coating Formulations: Why More Layers Don't Always Mean Better Protection
September 30, 2024
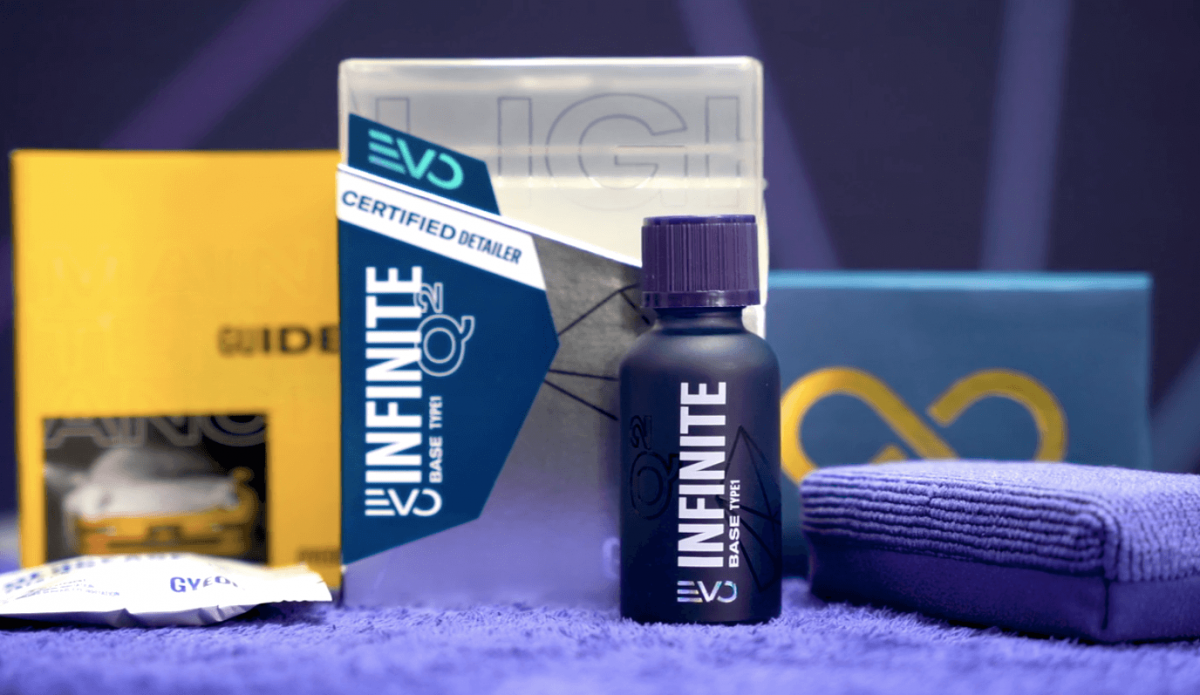
A common misconception in the world of ceramic coatings is that two layers automatically equates to better performance. The truth is much more nuanced than this. Professional ceramic coatings vary significantly in their formulations, properties, and durability ratings, regardless of the number of layers applied. A high-quality single-layer coating, properly applied, can offer exceptional protection and longevity.
What factors go into ceramic coating durability?
- Proper paintwork preparation: Thorough decontamination is essential for achieving optimal adhesion. This paint preparation involves a multi-stage process, beginning with a thorough decontaminating wash to remove loose dirt. Iron decontamination comes next, using a specialized chemical to dissolve embedded ferrous (iron) particles, normally caused by brake dust. A clay bar or mitt then physically removes any remaining bonded contaminants, leaving a perfectly smooth surface. While optional, polishing is highly recommended as it removes minor imperfections like swirl marks and light scratches, creating a flawless base for the coating and maximizing gloss, while also creating a fresh canvas for the ceramic coating application.
- Application conditions: All conditions must be met as per the manufacturer requirements in order to ensure optimal performance. This could include the appropriate temperature and humidity to avoid impacting the ceramic coating’s longevity. Direct sunlight, extreme heat, and cold temperatures should be avoided as they can negatively impact the coating's properties and longevity. A controlled environment, such as a clean garage or professional detailing shop, provides the ideal setting for ceramic coating application.
- Application technique: Coatings must be applied uniformly on thoroughly prepared paint. This can mean using a cross hatching or circular motion when applying to ensure that there is an even layer of the ceramic coating on the panel. Using the correct amount of ceramic coating can be the difference between an application with or without high spots. The coating must be leveled with excess removed to prevent streaking and ensure a flawless finish.
Are there advantages to two layer ceramic coatings opposed to single layer ceramic coatings?
The effectiveness of a ceramic coating isn't solely determined by the number of layers, but rather by the quality of the product itself and the precision of its application. While some manufacturers design their systems with a base coat and a top coat, this doesn't automatically translate to superior performance compared to a high-quality single-layer coating.
For instance, Gyeon Infinite Professional Ceramic Coating utilizes a two-layer system. The base coat provides the primary protective layer, focusing on adhesion and durability. The top coat adds an extra layer of gloss and enhances the hydrophobic properties, creating a more pronounced water-beading effect. This two-layer approach allows for a tailored approach, maximizing both protection and visual appeal.
However, advancements in ceramic coating technology have led to the development of incredibly durable single-layer coatings. C6 Ceramics' Nano Diamond coating, for example, offers exceptional hardness and longevity with just one application. Its advanced formulation incorporates nano-diamond particles for increased scratch resistance and a deep, glossy shine. This demonstrates that a single, well-formulated layer can rival the performance of a multi-layer system.
Ultimately, the best ceramic coating for your vehicle depends on your individual needs and priorities. A knowledgeable detailer will consider your lifestyle, driving conditions, and desired level of protection to recommend the most suitable product, whether it's a single-layer or multi-layer system. The key is to focus on the quality of the product and the expertise of the installer, rather than solely on the number of layers applied. A properly applied, high-quality single-layer coating can offer exceptional protection and longevity, often matching or exceeding the performance of a poorly applied two-layer system.
So then why doesn’t everyone formulate a single layer ceramic coating?
That's a great question, and it highlights the complexity of ceramic coating chemistry. Developing a single-layer coating that excels in all areas – durability, gloss, hydrophobicity, ease of application, and more – is a significant challenge. While some manufacturers have achieved this with advanced formulations, others opt for a multi-layer approach for several reasons:
Balancing Competing Properties: It's difficult to pack all desired characteristics into a single layer. Sometimes, the chemicals that enhance hardness and durability might detract from gloss or hydrophobicity. A multi-layer system allows manufacturers to separate these properties, optimizing each layer for a specific purpose. The base coat might prioritize adhesion and protection, while the top coat focuses on enhancing gloss and water-beading.
Tailoring Performance: A multi-layer system allows for greater flexibility in tailoring the coating's performance. By adjusting the composition of each layer, manufacturers can create coatings with varying levels of hardness, gloss, and hydrophobic properties to meet specific needs.
Simplifying Application: In some cases, a multi-layer system can actually simplify the application process. Applying thinner, individual layers can be easier to manage than a single, thicker layer, reducing the risk of high spots and unevenness.
Marketing and Perceived Value: Let's be honest, the perception of "more layers = better protection" persists in the market. Some manufacturers might leverage this perception by offering multi-layer systems, even if a single-layer formulation could achieve comparable results.
While single-layer coatings are becoming increasingly sophisticated, the multi-layer approach remains a viable option for achieving a balanced and tailored performance profile. Ultimately, the best approach depends on the specific chemistry and desired characteristics of the coating.
What are some common mistakes while applying ceramic coatings?
Ceramic coatings require a high level of experience in order to perform properly. Many detailers have the ability to apply a ceramic coating at a satisfactory level, but the experience required to apply the same coating at an expert level can be the difference between a good and great application.
Common issues that happen amongst different levels of detailers include high spots, improper decontamination, use of the wrong towels, working outside of ideal conditions, or lack of proper curing. Avoiding and troubleshooting issues comes with the territory of a great ceramic coating application. Don’t settle, compromising the durability and effectiveness of the ceramic coating.
How can I ensure that I’m picking the best ceramic coating?
We recommend choosing a reputable ceramic coating installer for your ceramic coating, certified with their manufacturer’s certification. We believe a great detailer will understand your needs and work with the newest and best products, knowledgeable about the unique features each has to offer. Westchester Auto Detail offers an updated and handpicked ceramic coating offering to exceed the industry standard.
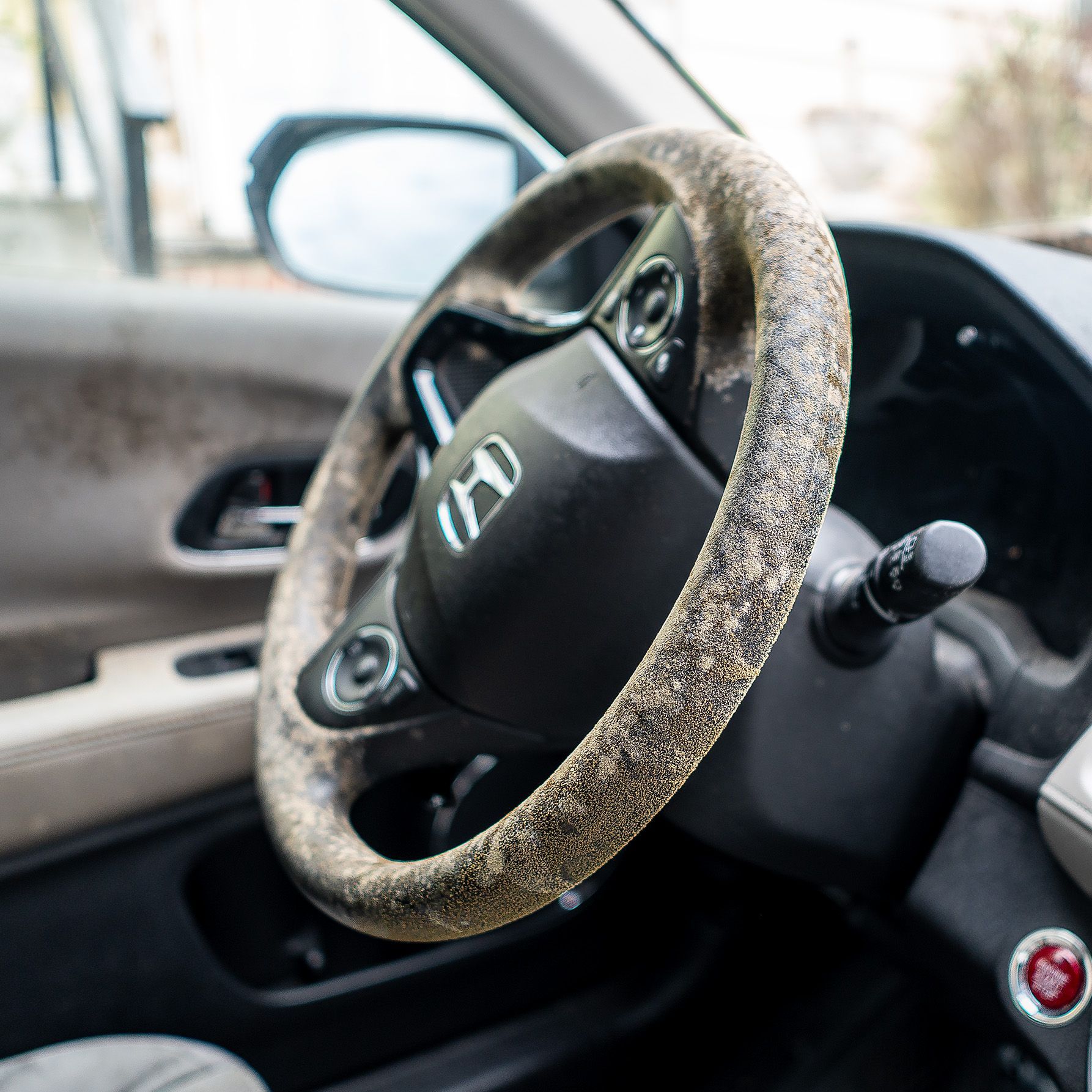
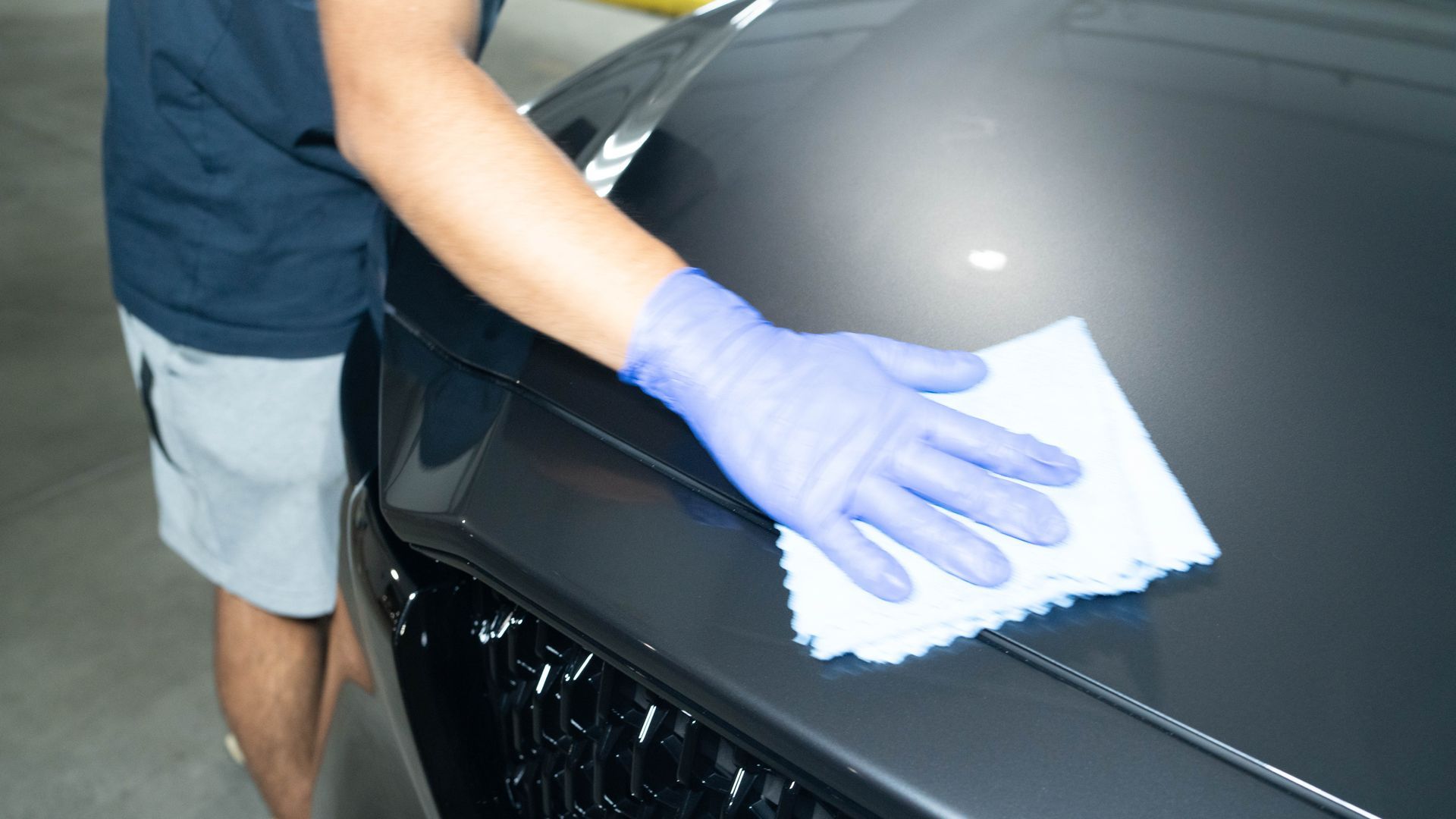
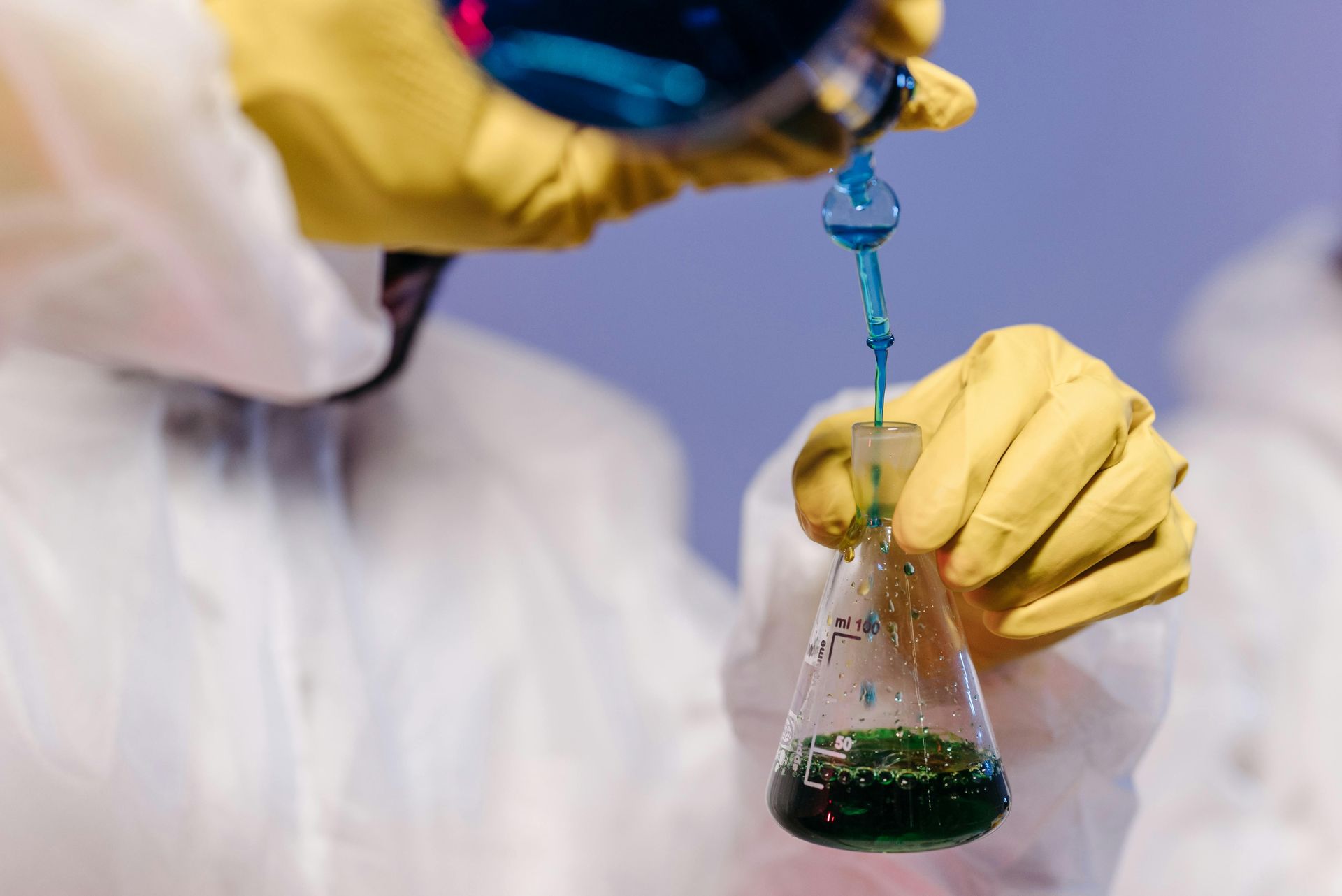