Prep Work is Key: The Benefits of Correcting Paint Before Applying a Ceramic Coating
January 17, 2024
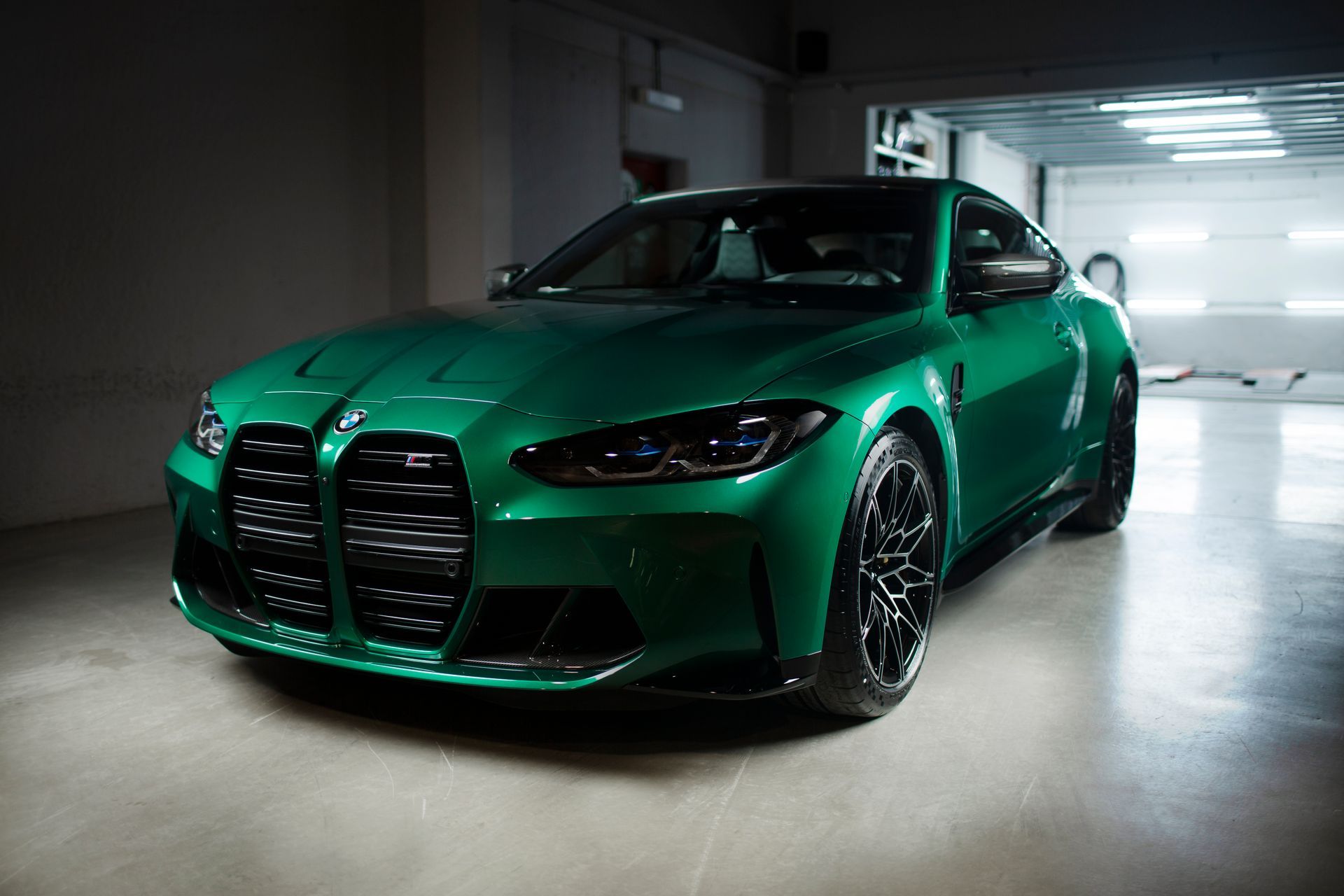
Do I Need Paint Correction Before Ceramic Coating?
When considering a ceramic coating, one of the most debated questions is: "Do I need paint correction first?" There's no straight answer, but paint correction provides important benefits that can maximize the results and longevity of your ceramic coating.
Why Paint Correction is Recommended
There are a few key reasons why professional ceramic coating manufacturers and installers recommend paint correction prior to coating:
Manufacturer Requirements
Most major ceramic coating brands require paint correction as part of their application process. This ensures the coating can bond optimally to a fresh layer of clear coat for proper adhesion and durability.
Remove Surface Imperfections
Even on a new car, the paint can have minor swirls, scratches, and defects from delivery prep and transport. Paint correction polishes away these flaws to ensure a perfectly smooth finish for the coating.
Enhance Coating Bond
Polishing eliminates contaminants that could interfere with bonding, while exposing a fresh layer of clear coat allows superior adhesion. This enhances durability.
Extend Coating Lifespan
Like waxes and sealants, ceramic coatings last longer on a corrected surface. The smoother the canvas, the longer-lasting the finish.
Can You Apply Without Paint Correction?
Technically, yes you can install a ceramic coating without paint correction. However, this goes against best practices and manufacturers' guidelines. Here are some downsides of skipping paint correction:
Reduced Bonding
Surface contaminants and oxidation may still be present, preventing optimal bonding between the paint and coating.
Shortened Lifespan
The coating won't adhere as strongly or last as long on paint that hasn't been smoothed and prepped through polishing.
Existing Flaws Won't Be Removed
Light scratches, swirls and etching will still be visible in the paint underneath the coating.
Difficult Removal If Issues Arise
Ceramic coatings bond tightly to paint. Flawed applications that must be removed can be much more tedious without a fresh polish underneath.
Conclusion: Better Safe Than Sorry
While you *can* ceramic coat without paint correction, the results likely won't meet your expectations for durability and appearance. For optimal bonding and longevity per manufacturer specifications, paint correction is a smart investment.
Rather than risk a coating that underperforms or fails prematurely, trust the experts at Westchester Auto Detail to properly prepare your paint first. We'll ensure you get the most out of your ceramic coating for long-lasting protection and shine.
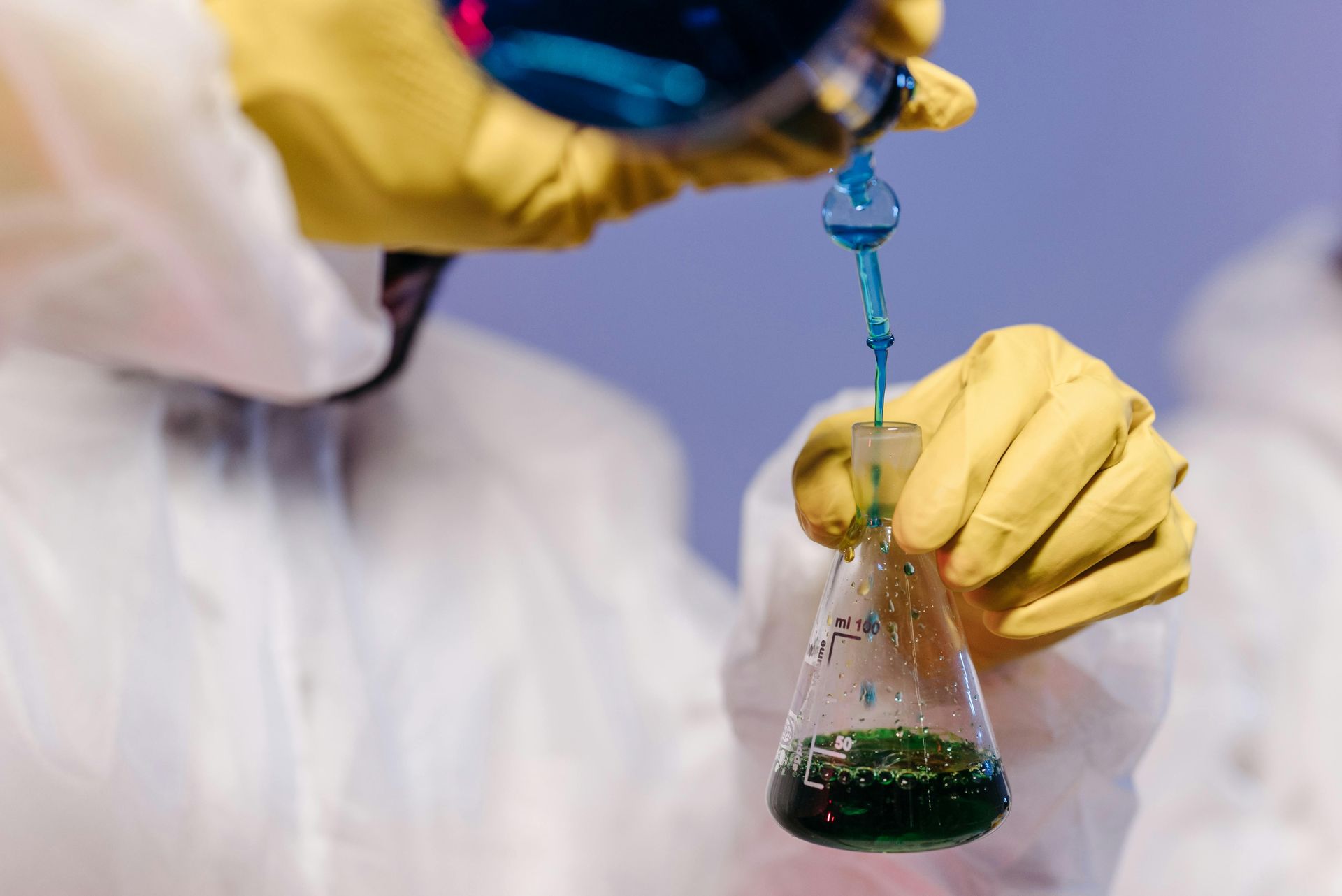
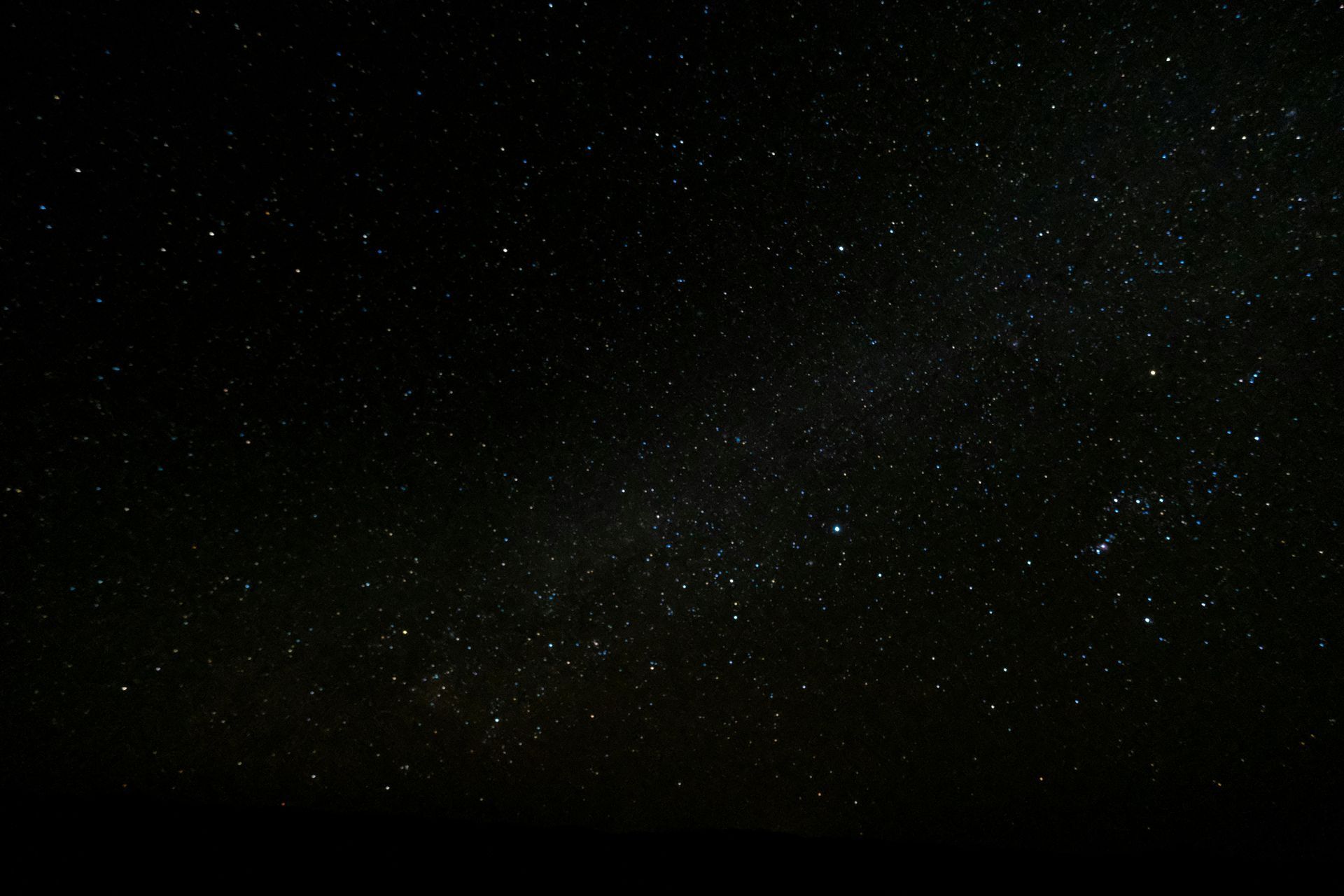